UNO MINDA uses altair® simlab® to maintain deviation in on-board ev chargers to less than 5%
About the Customer
UNO MINDA is a global leader in automobile component manufacturing and supply. The group began operations in 1958 and is today one of the leading companies that delivers proprietary automotive solutions to original equipment manufacturers (OEMs) and Tier 1 vehicle manufacturers. UNO MINDA has several manufacturing facilities and research and development centers in India, and the South Asian, South American, European, and ASEAN regions.
Their Challenge
What Does Innovation Look Like at UNO MINDA?
Rapid innovation and the generation of modern-day products are the need of the hour. In the last decade, the automotive industry has seen a rapid transformation from vehicles powered by internal combustion engines to electric vehicles (EVs). Major Tier 1 automobile manufacturers and OEMs are now prioritizing EVs. Within EVs, there are multiple components like on-board chargers, DC-DC converters, and vehicle management systems. The most challenging part of these products is their thermal management. These products’ compact size and low wattage also add additional hurdles. Due to these constraints, components must be designed so they deliver optimal thermal and mechanical performance. In addition, many other challenges arise while designing printed circuit board (PCB) models, including component layouts, thermal management, and the components’ cooling requirements. Designers must consider all these factors and ensure the products’ durability and low maintenance.
To tackle these challenges, UNO MINDA employs a diverse approach. They use innovation in materials, simulations, and methodologies, and incorporate industry requirements to create the best products possible.
The Role of Digital Simulation in Product Innovation at UNO MINDA
Making a prototype for each design consumes a lot of time and increases end products’ costs. Digital simulation, on the other hand, lets teams test various designs much quicker. This accelerates the product design process while also driving innovation. UNO MINDA utilizes Altair® SimLab® for thermal management by performing different design of experiments (DoEs). They also perform multiple sensitivity analyses. Once they’ve analyzed all the data, they select the best designs from a list of often more than 100 DoEs. These select few designs are then further validated and tested for final selection.
SimLab enables the use of all these different tools in one place, like a system-level simulation, which UNO MINDA is looking forward to incorporating in the future,” said Shantaram Jadhav, Senior Principal Lead UNO MINDA
UNO MINDA’s Main Product Development Challenges
UNO MINDA uses SimLab to design the on-board charger, which charges the EV’s battery. The main requirements for the on-board charger are that it must be compact and accelerate the charging process in a short period of time. However, obtaining optimal thermal management while both maintaining a compact size and reducing the charging period is a very complex requirement. These requirements are complex because when designing a product with high power density, other factors such as signal integrity, power integrity, and EMI/EMC must also be optimized. All this must be managed while making sure it’s an electrothermal approach, ensuring both thermal and electrical performance, and maintaining structural rigidity.
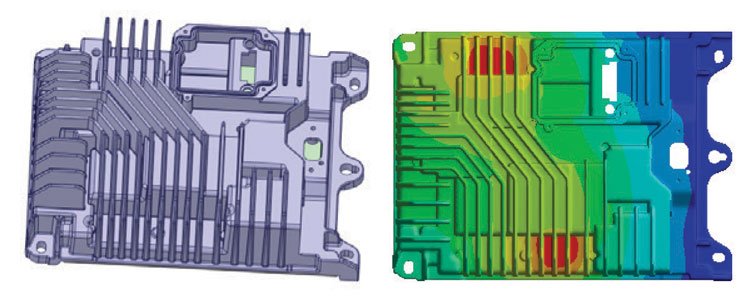
Our Solution
DesignTech, an Altair partner, introduced UNO MINDA’s team to SimLab, which offers a comprehensive solution to the challenges described above. SimLab uses an innovative approach and offers different meshing strategies. Also, Altair® PollEx™, a PCB design and verification tool that captures trace information and utilizes it for specific PCB-level simulation, is crucial in obtaining accurate results in electromechanical analysis.
SimLab is also useful in thermal testing, which allows UNO MINDA to identify the critical heat transfer path and PCB hotspots while also obtaining accurate virtual simulation results in terms of temperature and the heat flux plot. “Identifying hotspots with SimLab enables us to improve the heat conduction path from PCB components to the ambient environment,” said Shantaram Jadhav, senior principal lead, UNO MINDA.
Results
UNO MINDA’s main objective in designing the on-board charger was to manage thermal conductivity and maintain low temperatures. With SimLab, they were able to check the temperature distribution across different components and assembly levels. They could also observe the temperature gradient and analyze the temperature distribution across the product body.
Thus, UNO MINDA obtained crucial information from this analysis, such as identifying the critical heat transfer path concerning thickness, thermal conductivity, and cooling systems. These results enabled UNO MINDA to improve its designs. After comparing the results obtained from actual physical tests and CAE simulations, UNO MINDA found a 10% deviation. These results are helping them work further and improve their designs to reduce the deviation to less than 5%.
UNO MINDA’s Future Plans to Use Altair Software
Modern products have complex, multifaceted requirements. In the future, UNO MINDA is hoping to use multiple Altair tools to consider various factors, such as Altair® Feko® and Altair® Flux® for high and low frequency analysis respectively, Altair® MotionSolve® for multibody dynamics, and PollEx for PCB-level thermal analysis.
In system-level simulations – when UNO MINDA chooses electrical circuit tools like EMI/ EMC, thermal management, and mechanical structure performance tools – they are hoping to integrate all these requirements to get real-time or virtual simulation performance.
To learn more, please visit altair.com