As the global shift towards electric vehicle (EV) production accelerates, vehicle manufacturers are navigating the complexities of this emerging industry. Meanwhile, governments are responding by introducing regulations to ensure safety and quality in EV assembly.
An EV is a complex system of mechanical, electronic and mechatronic parts, such as the battery, motor, inverter and e-drive, which are connected by a large cluster of connectors and wires. These components account for more than 50% of the vehicle’s total weight and cost.
While EVs offer more efficient utilisation of energy, the incorrect assembly of battery packs can lead to safety and operational issues, as evidenced by numerous incidents worldwide of vehicles catching alight.
Emerging safety standards
To mitigate these risks, governments are introducing new regulations, such as the AIS-156 standard in India. This standard focuses on safety requirements for EVs, particularly battery packs or Rechargeable Electrical Energy Storage Systems (REESS).
The regulations advocate for a transparent, data-driven assembly process. Manufacturers are required to keep a traceability document for each REESS, detailing the components used, including cells, battery management system (BMS), charger, and corresponding parts serial or batch numbers.
In the event of an incident or product recall, this traceability document allows manufacturers to track the origin, quality, and performance of individual components within the battery pack, and take corrective action.
The ultimate goal is to foster consumer confidence in EVs through proven compliance with safety standards.
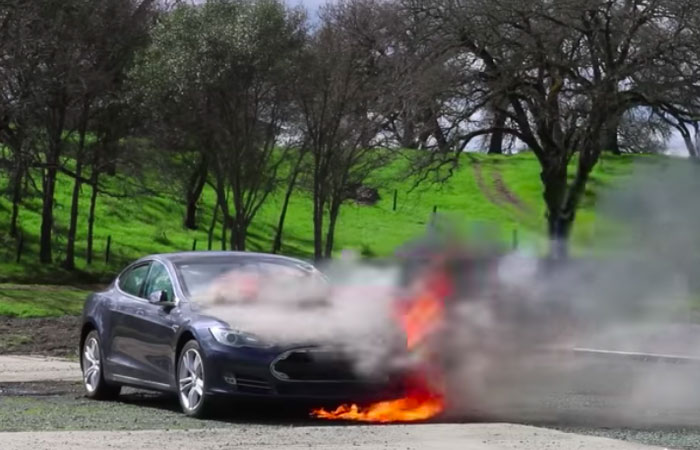
Supporting complex assembly
While manufacturers invest significant resources in developing products and building prototypes for certification, the attention to detail and expertise shown in these initial stages does not always carry through into the production process.
This is because many EV manufacturing facilities, including startups, employ semi-skilled and inexperienced operators. Given the revolutionary and complex nature of EVs, there is a pressing need for extensive operator training.
However, the rapid increase in production to meet market demand often leaves insufficient time for upskilling, leading to manufacturing errors and costly product recall campaigns.
Therefore, a process security system that ensures product quality and operator safety is crucial.
Practical solutions
A practical starting point is a step-by-step operator guidance system that allows workers to follow the set process for assembling each type of battery or variant via an interactive touchscreen, thereby reducing training time.
In addition to providing operator guidance, Jendamark’s digital manufacturing solution, ODIN Workstation, integrates with station hardware, such as tightening tools, PLCs and testing equipment, to ensure correct assembly every time. The use of advanced AI computer vision systems to control the correct part fitment and tightening sequence further ensures the quality and integrity of battery packs.
When it comes to ensuring the efficiency and longevity of EV battery packs, it is essential to assemble only the same grade of cells into a single module. These modules are then assembled into a battery pack. Assembling only cells of the same grade in a single module is necessary because the battery management system (BMS) charges and discharges each module as a single unit.
For our customers, we have automated the grading of cells by measuring their open circuit voltage (OCV) values. ODIN Workstation records these values and cell grades and uses this data to correctly assemble battery modules and packs
Furthermore, ODIN Workstation integrates with testing machines to meet additional requirements listed in standards like AIS-156, which include testing of battery management systems, thermal management, and charge-discharge quality of battery packs. All this data is stored and can be accessed using the serial number of each battery pack.
Looking ahead
As the global EV market expands and competition intensifies, data-driven process control will become a standard requirement for all vehicle manufacturers. Car makers are already enhancing their manufacturing processes and investing in a mix of automation and digital process security on their assembly lines to ensure the safety of people and products.
source: Jendamark Automation